Робототехнические комплексы для возведения объектов из мелкоштучных материалов
Библиографическое описание:Шутин, Д. В. Робототехнические комплексы для возведения объектов из мелкоштучных материалов / Д. В. Шутин, А. В. Малахов. — Текст : непосредственный // Молодой ученый. — 2015. — № 11 (91). — С. 474-477. — URL: https://moluch.ru/archive/91/19473/ (дата обращения: 28.01.2023).
В настоящее время рост объемов возводимых зданий и сооружений ведет к необходимости привлечения значительного количества рабочей силы для выполнения строительно-монтажных работ, что в свою очередь поднимает проблему обеспеченности квалифицированными кадрами как инженерных, так и рабочих профессий. При этом нередко рабочие имеют недостаточную квалификацию, что приводит к допущению грубых ошибок, нарушению технологии и получению некачественной продукции, а также невыполнению сроков ввода объекта в эксплуатацию. Одним из направлений решения данной проблемы и совершенствования строительного процесса в целом является внедрение автоматизированных и роботизированных комплексов.
1. Повышение качества продукции. Применение автоматизированных технических комплексов значительно снижает риск совершения ошибки человеком, что позволяет строго соблюдать нормативы и требования к качеству возводимых объектов.
2. Сокращение сроков строительства и приведенных затрат. Автоматизация циклических операций, являющихся одними из основных в процессе возведения объектов из мелкоштучных материалов, позволяет добиться повышения производительности работ, сокращая тем самым временных затраты на возведение объектов.
3. Снижение физической нагрузки на человека в производстве. Механизация и автоматизация технологических процессов является существенным фактором, улучшающим условия труда и, как следствие, способствующим повышению его производительности.
Существующее многообразие робототехнических комплексов для возведения объектов из мелкоштучных материалов позволяет выявить некоторые типичные конструктивные и функциональные особенности известных решений и создать таким образом классификацию по ряду признаков. По способу размещения соответствующих комплексов на строительном объекте можно выделить следующие категории.
1. Стационарные комплексы — в общем случае представляют собой каркас, выполняющий функцию направляющих для перемещения исполнительного органа, непосредственно осуществляющего монтаж конструкций [2, 3]. Подобные комплексы обычно функционируют по принципу, сходному с используемым в 3D-печати, когда объект постепенно формируется за счет нанесения новых слоев поверх уже уложенных, постепенно увеличиваясь в высоту. Каркас такого комплекса стационарно устанавливается на месте возведения объекта до начала непосредственного процесса строительства таким образом, чтобы диапазон перемещения исполнительного органа полностью перекрывал площадь возводимого объекта. После окончания монтажа комплекс демонтируется. Такие решения позволяют значительно ускорить процесс строительства объекта по сравнению с неавтоматизированным подходом и получать высокую точность при возведении, поскольку элементы конструкции привязаны к местности при их монтаже и позволяют осуществлять точное позиционирование исполнительных органов.
2. Передвижные комплексы — в общем случае представляют собой системы исполнительных органов, непосредственно осуществляющих возведение объекта из мелкоштучных материалов, которые устанавливаются на подвижное шасси. Шасси передвигается вдоль периметра возводимого объекта по грунту, рельсам или иной заранее подготовленной поверхности и осуществляет монтаж конструкций [4–7]. Мобильность таких комплексов неизбежно ставит вопрос о снабжении систем исполнительных органов необходимыми строительными материалами.
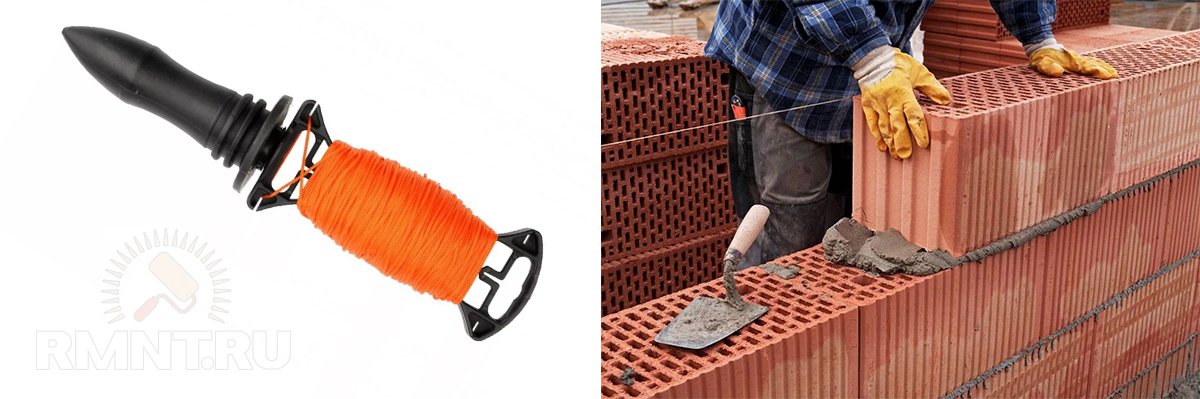
3. Многокомпонентные комплексы — в общем случае представляют собой множество однотипных устройств, действующих на возводимом объекте одновременно и в прямом или опосредованном групповом взаимодействии между собой. Каждое из устройств обладает высокой мобильностью, которая обеспечивается компактными размерами и практически полной автономностью в передвижении по строительной площадке. Идея таких комплексов заимствована из природных биологических систем — обычно, групп насекомых, которые сообща возводят обширные укрытия (термиты, муравьи, осы), как, например, в [10].
Анализ имеющихся конструктивных решений в области робототехнических комплексов для возведения объектов из мелкоштучных материалов, позволяет также выделить два базовых подхода к конструкции исполнительных органов, непосредственно осуществляющих укладку строительных материалов, различающихся по типу используемого в них механизма:
– исполнительные механизмы манипуляторного типа — в таких решениях для формирования кладки используется исполнительный орган-манипулятор, функционально приближающийся к руке человека.
– специализированные исполнительные механизмы — в таких решениях для формирования кладки используется специально сконструированный механизм, к которому за счет сопроводительных систем подачи поступают строительные материалы. При этом, в сравнении с манипуляторными механизмами снижается гибкость процесса возведения, что может накладывать определенные ограничения на сложность осуществляемых типов кладки. Вместе с тем, специализированные механизмы позволяют значительно повысить скорость кладки за счет отсутствия необходимости переноса каждого элемента от места складирования к месту монтажа. Это позволяет успешно использовать их на объектах относительно простой конфигурации, но состоящих из значительного объема мелкоштучных материалов, что позволяет значительно ускорить возведение конструкции по сравнению с ручным трудом.
Анализ особенностей существующих решений совместно с требованиями современного строительного процесса позволяет сделать вывод о том, что сфера пересечения строительства и робототехнических технологий обладает значительным потенциалом для новых исследований и разработок, результаты которых могут быть востребованы в первую очередь на российском рынке, на котором наблюдается дефицит как предложения, так и практического применения автоматизированных строительных комплексов, в том числе для возведения объектов из мелкоштучных материалов. Актуальными направлениями развития специальной техники в данном направлении являются повышение степени автоматизации процесса строительства, повышение производительности и расширение функциональных возможностей роботизированных строительных комплексов, что позволит эффективно решать отмеченные ранее задачи. На основании проведенного анализа можно сформировать ряд требований, которые предъявляются к современным робототехническим комплексам для возведения объектов из мелкоштучных материалов, которые могут быть востребованы в современной строительной сфере в России и за рубежом.
1. Комплекс должен быть многофункциональным, т. е. обеспечивать полный цикл работ при устройстве кладки вне зависимости от его конструктивного решения и способа размещения на строительной площадке.
2. Комплекс должен быть универсальным, т. е. его конструкция и функциональные возможности должны позволять эффективно использовать его при возведении объектов различной сложности, высотности, объемности и т. п. При этом комплекс должен иметь возможность выполнения различных видов кладки: сплошной или колодцевой, различной толщины, выполнение эркеров, круглых стен и т. д.
3. Комплекс должен быть гибким и высокомобильным, т. е. иметь возможность быстрого ввода в эксплуатацию при размещении на объекте или перемещении на новые участки работ, а также оперативной переналадки.
4. Комплекс должен иметь более высокую производительность и обеспечивать меньшее количество ошибок в сравнении с живой рабочей силой при одинаковых объемах производства работ.
5. Комплекс должен быть простым в эксплуатации и обслуживании, что позволит использовать минимальное количество обслуживающего персонала и в свою очередь приведет к снижению затрат и удешевлению строительного производства.
Разработка мобильных робототехнических комплексов для возведения объектов из мелкоштучных материалов, отвечающих таким требованиям, а также проведение исследований, обеспечивающих возможность создания таких комплексов, является важной научной и практической задачей, решение которой лежит в рамках междисциплинарного взаимодействия сфер строительства, машиностроения и информационных технологий.
Литература:
1. Оборудование для автоматизированной кладки кирпичных стен МКСК [Электронный ресурс]. — URL: http://a-v-a.ru/index.php/real-projects/story/kamen.
2. Springer Handbook of Automation / Под ред. Shimon Y. Nof, Springer-Verlag Berlin Heidelberg, 2009. — 1888 c.
3. Marc Howe. Robots on the Verge of Invading Construction Sites [Электронный ресурс]. — URL: https://sourceable.net/.
4. P. S. Lawrence, P. Nathan, C. T. Charles. Brick Laying System. — Патент США US2015082740 (A1), 2015.
5. B. Dornsiepen. Mobile building-block-laying masonry machine. — Патент Германии DE2406588 (A1), 1975.
6. N. Francois. Robotic Device for Building a Wall from Construction Blocks. — Патент WO2009044002 (A1), 2009.
7. G. Pritschow, M. Dalacker, J. Kurz, J. Zeiher. A Mobile Robot for On-Site Construction of Masonry. — Proceedings of Conference: Intelligent Robots and Systems, т. 3. — С. 1701–1707.
8. M. J. Pivac, M. B. Wood. Automated Brick Laying System for Constructing a Building From a Plurality of Bricks. — Патент США US2009038258 (A1), 2009.
9. J. Dyson. AMPRO BR — Bricklaying Robot [Электронный ресурс]. — URL:. http://www.jamesdysonaward.org/ru/projects/ampro-br-bricklaying-robot/.
10. J. Werfel, K. Petersen, R. Nagpal. Designing Collective Behavior in a Termite-Inspired Robot Construction Team // Science, т.343. — 2014. — № 6172.
Основные термины (генерируются автоматически): комплекс, материал, возведение, решение, общий случай, строительная площадка, автоматизация процесса строительства, исполнительный орган, строительная отрасль, точное позиционирование.
Робот, который может укладывать 1000 кирпичей в час
С переходом к Индустрии 4.0 роботы начинают появляться в строительной отрасли. А учитывая нехватку рабочей силы во всех странах, неудивительно, что новаторы обращаются к робототехнике, чтобы заполнить пробел в квалифицированных профессиях. Двумя наиболее обсуждаемыми строительными роботами являются робот-каменщик Hadrian X, разработанный FBR в Австралии, и SAM100, созданный Construction Robotics в США. Вот как эти два робота меняют одну из самых традиционных областей строительства.
Самый быстрый робот-каменщик
Робот-каменщик Hadrian X попал в заголовки газет в 2016 году, когда он уложил 1000 кирпичей в час. Чтобы понять, как это можно сравнить, каменщики обычно могут укладывать 300-500 кирпичей в день, при этом рекорд составляет 914 кирпичей, уложенных за час. С тех пор FBR дорабатывала как робота, так и материалы, с которыми он работает, используя специально разработанные блоки, которые соединяются друг с другом и в 12 раз больше, чем традиционный кирпич. Раствор, используемый с этими блоками, также был специально разработан для использования с роботом и высыхает за 45 минут, по сравнению с 1-2 днями для традиционного раствора. Hadrian X может укладывать 200 таких блоков за час, и FBR стремится увеличить этот показатель.
Робот использует 30-метровую стрелу, которая доставляет кирпичи на укладочную головку, а также может резать, шлифовать, фрезеровать и направлять кирпичи по размеру. Можно использовать кирпичи разных размеров, от кирпича стандартного размера до крупных блоков, разработанных FBR. Кирпичи необходимо вручную загрузить в робота, после чего он сможет работать автономно. А благодаря своей телескопической стреле он также может строить криволинейные стены и укладывать кирпичи по углам.
В настоящее время запатентованная система управления использует данные CAD и 3D-моделей и использует декартовы координаты и параметрический расчет для определения места размещения каждого кирпича. С появлением информационного моделирования зданий (BIM) и 3D-моделирования нетрудно представить себе время, когда роботы-каменщики, такие как эти, смогут получить доступ и использовать модель BIM, чтобы определить, как и где класть кирпичи. Хотя Hadrian X в настоящее время недоступен в продаже, когда он будет выпущен, FBR заявляет, что типичный дом можно построить всего за два дня с помощью их робота.
Устранение ручного труда при кладке кирпича
Подход Construction Robotics немного отличается от подхода FBR. Вместо того, чтобы автоматизировать весь процесс, SAM100 (полуавтоматический каменщик) работает вместе с человеком, помогая исключить часть ручного труда из процесса. С помощью SAM100 можно укладывать до 3000 кирпичей в день, что делает строительство в шесть раз быстрее, чем каменщик, работающий самостоятельно. Этот робот поднимает кирпичи, наносит на них раствор и кладет кирпичи на стену. Затем каменщик, работающий вместе с роботом, сглаживает излишки раствора. Это значительно ускоряет процесс укладки, а также улучшает здоровье и безопасность рабочих за счет сокращения ручных операций.
Интересные разработки для строительства и BIM
Учитывая, что потребность в квалифицированных каменщиках и в большем количестве домов быстро растет во всем мире, автоматизация процесса кладки кирпича для ускорения массового строительства является очевидным ответом. И поскольку переход к строительным роботам продолжает развиваться, вполне вероятно, что BIM будет играть все возрастающую и неотъемлемую роль в процессе строительства как средство предоставления строительной информации для этих новых технологий. Одно можно сказать наверняка — цифровая автономная эра действительно наступила в строительной отрасли.
youtube.com/embed/G_Pj2GI6-xc?feature=oembed” frameborder=”0″ allow=”accelerometer; autoplay; clipboard-write; encrypted-media; gyroscope; picture-in-picture” allowfullscreen=””>
Краткая история роботов-каменщиков
Это захватывающее время для строительного сектора. Мы видим, как многие цифровые, технологические и инновационные решения начинают внедряться и влиять на
наша промышленность.
Тем не менее, стоит отметить, что отрасль уже давно стремится к большей автоматизации и эффективности — как видно из этого кадра кладочный станок 1967 г.
Выше : «Моторный каменщик» 1967 года в действии, которому помогают каменщики (изображение предоставлено British Pathé).
Названный «Motor Mason», он двигался по рельсам, проложенным параллельно стене, нанося раствор и кладя кирпичи по ходу движения.
Для его обслуживания требовалось три человека: один квалифицированный каменщик, который обеспечивал качество работы, и два чернорабочих, которые «кормили»
роботы кирпичи и раствор, позиционируя его по мере необходимости.
Описанный как «современный метод, примененный к старому ремеслу», механизированный каменщик предположительно был в пять-десять раз быстрее, чем люди, но он не прижился. Возможно он был слишком громоздким и подвержен поломкам или не мог справиться с более сложными формами зданий, такими как углы и окна.
Выше : патент США 1904 года, выданный Джону Томсону на механического каменщика (изображение предоставлено Патентным бюро США).
Что еще более удивительно, так это то, что такая машина была задумана не впервые.
По данным Патентного ведомства США, первое устройство для кладки кирпича было запатентовано в 1904 году Джоном Томсоном. Цель машины была такой же, как у современной кирпичной кладки. роботы: для ускорения процесса строительства и повышения эффективности. Конечно, эта машина не произвела революцию в отрасли.
«Первое устройство для кладки кирпича было запатентовано в 1904 году».
первая работоспособная машина.
Возьмем, к примеру, SAM, сокращенно от «Полуавтоматический каменщик», разработанный Construction Robotics при поддержке Национального научного фонда США.
SAM, представленный в 2015 году, работает по тому же принципу, что и Motor Mason, но его роботизированная рука позволяет более точно размещать и наносить раствор.
Выше : SAM может укладывать до 3000 кирпичей в день по сравнению с 1000 в день квалифицированным каменщиком (изображение предоставлено Национальным научным фондом).
Несмотря на то, что SAM может укладывать около 3000 кирпичей в день, обнаруживать и исправлять различия между цифровыми планами и реальной строительной площадкой, руководство и опыт рабочих для подачи сырья, очистки излишков раствора и отделки углов, а также других задач, связанных с более сложная кирпичная кладка.
Тем временем швейцарские исследователи разработали «In-Situ Fabricator» в Национальном центре компетенций в области исследований ETH Zurich (NCCR) Digital Fabrication. В следующем видео можно увидеть, как робот укладывает кубики в более свободной форме, расширяя формальные возможности, предлагаемые SAM. Однако,
In-Situ Fabricator (также представленный в 2015 году) (пока) не наносит раствор или любое другое связующее вещество.
Выше : In Situ Fabricator, разработанный исследователями ETH Zurich в Швейцарии (видео предоставлено NCCR Digital Fabrication).
Другой робот, который в настоящее время находится в разработке, — это Hadrian X австралийской компании Fastbrick Robotics, который сочетает в себе два подхода. Его длинный, выдвижной, многоосевой рука может укладывать кирпичи на фундамент, наносить клей и вытягивать кирпичи из внутреннего контейнера для хранения.
Утверждается, что после ввода в эксплуатацию Адриан Х сможет полностью построить дом всего за два дня.