видео-инструкция как укладывать на пол своими руками, как класть арт-винил, чем обработать, технология, фото и цена
Статьи
Практически любой тип декоративного напольного покрытия нуждается в наличии ровного и гладкого основания. Укладка фанеры гарантирует такие условия. О том, как выполнить её правильно и пойдёт речь далее.
Процесс монтажа фанерного пола
Общие положения
Для начала давайте немного поговорим о самой древесно-слоистой плите, чтобы выяснить причину её популярности в данной строительной области.
Достоинства
Данный вид материала представляет собой некоторое нечётное количество листов деревянного шпона, которые надёжно склеены между собой с помощью специального фабричного оборудования.
Отсюда и следующие характеристики:
- Красивый внешний вид. При желании высокосортную фанеру можно уложить и в качестве чистового слоя, отшлифовав и покрыв лаком;
Фото чистового фанерного пола
- Абсолютно ровная и гладкая поверхность.
Это наиболее важный фактор для нашего случая, благодаря которому возможен монтаж даже таких капризных декоративных материалов, как плитка, ламинат и Арт Винил;
Укладка Арт Винила на фанеру осуществляется достаточно просто благодаря её идеально гладкой поверхности
- Низкая теплопроводность. Дополнительное утепление половой конструкции никогда не будет лишним;
- Звукоизоляционные свойства. Позволит снизить грохот посуды, упавшей, например, на звонкий кафель;
- Высокие прочностные и водоотталкивающие качества. Всё дело в клеевых прослойках, которые увеличивают и прочность древесины, и её влагостойкость, что очень важно для чернового слоя любого пола;
- Приемлемая цена. Стоимость древесно-слоистой плиты вполне доступная для простого обывателя;
- Простота обработки. Фанера легко пилится, сверлится, шлифуется и фрезеруется;
Шлифовка фанеры в домашних условиях
- Небольшой вес. Не оказывает существенной нагрузки на перекрытия.
Выполнение монтажных работ
Перед тем, как укладывать на пол фанеру, её нужно приобрести:
Этап №1: выбор древесно-слоистой плиты
Это весьма ответственный процесс, так как рассматриваемый материал имеет множество разновидностей:
- В первую очередь следует определиться с маркой:
Маркировка | Пояснения |
ФК | Для склеивания шпона применяется карбамидная смола, что делает изделие пригодным для эксплуатации в жилых помещениях и наделяет его приемлемой влагостойкостью |
ФСФ | Здесь уже используется фенольная смола, которая гарантирует высокие водоотталкивающие свойства, но также отличается и значительной токсичностью |
ФБ | Все древесные слои в данном случае пропитываются бакелитовым лаком, благодаря чему готовая секция обладает чрезвычайно высокими эксплуатационными качествами, выдерживающими и северные морозы, и жар тропических областей, и даже воздействие солёной морской воды |
ФОФ | Ламинированный образец, предназначенный специально для сборки предметов мебельного интерьера |
Совет: для пола лучше всего подойдёт марка ФК, так как ФСФ слишком токсична для укладки в жилых помещениях, а ФБ и ФОФ обладают значительно более высокой стоимостью за счёт качеств, которые абсолютно не будут востребованы в нашем случае.
ФК – идеальный выбор для создания чернового основания
- Порода дерева также имеет немаловажное значение:
Древесина | Особенности |
Хвойные породы | Повышенная влагостойкость, уступает по прочности |
Лиственные породы | Более высокая стойкость к механическим воздействиям |
Совет: в этом вопросе рекомендуется сделать ставку на прочностные характеристики, так как влагостойкость можно усилить и иными методами, а вот если основание не выдержит оказываемых нагрузок, то это обернётся катастрофой.
Образцы берёзовой древесно-слоистой плиты
- С сортом также лучше не прогадать:
Сорт | Краткое описание |
1 | Дефекты практически отсутствуют |
2 | Допускается наличие сросшихся сучков |
3 | Кроме сросшихся сучьев возможно наличие отверстий в случае их выпадения |
4 | Возможно значительное количество изъянов |
Примеры различных сортов фанеры
Совет: стоит остановить свой выбор между вторым и третьим сортами.
За первый переплачивать точно нет смысла, так как его практически идеальную поверхность всё равно не будет видно после укладки чистового покрытия. Внутренняя же часть, отвечающая за эксплуатационные показатели изделия, у всех типов фанеры одинаковая. А четвёртый может потребовать дополнительного шпаклевания с целью устранения неровностей, способных повлиять на декоративную облицовку.
- Уровень содержания формальдегидов определяет экологичность продукта, в наших магазинах, как правило, встречаются два варианта:
Символ | Количество токсинов, мг/100 г | Комментарии |
Е1 | 10 | Допускается использование в жилых помещениях |
Е2 | 10-30 | Не допускается использование в жилых помещениях |
- Кроме всего прочего обратите внимание и на шлифовку:
Обозначение | Пояснение |
НШ | Шлифовка отсутствует вовсе |
Ш1 | Шлифовка присутствует с одной стороны |
Ш2 | Шлифовка присутствует с обеих сторон |
Древесно-слоистая плита НШ самая дешёвая
Совет: здесь наилучшим вариантом станет выбор моделей с маркировкой Ш1.
НШ может потребовать выполнения шлифовки самостоятельно, а это дополнительные трудовые и финансовые затраты. А Ш2 ляжет одной обработанной стороной вниз, что будет попросту расточительно.
Таким образом, можно подытожить, что лучше всего для выравнивания пола подойдёт фанера ФК-2Е1Ш1.
Этап №3: подготовка основания
Здесь два варианта:
- Если у вас бетонный пол, то проверьте наличие перепадов с помощью ватерпаса. Если они слишком резкие, то стоит залить выравнивающую стяжку;
- Если же пол дощатый, то необходимо его перебрать на выявление гнилых и повреждённых элементов. При наличии большого количества недееспособных досок выполняется укладка фанеры на лаги.
Этап №2: порезка и разметка
Распилка листа фанеры
Далее инструкция предполагает порезку секций.
Для чего это нужно?
- Во-первых, небольшими листами легче оперировать;
- Во-вторых, таким методом проще будет создать сеть компенсационных швов.
Наиболее удобно приобрести листы 125 см на 125 см и разрезать их на 4 равных квадрата с примерной стороной в 60 см. Порезку можно осуществлять как дисковой пилой, так и электрическим лобзиком.
Далее поступаем так:
- Раскладываем получившиеся куски древесно-слоистой плиты в шахматном порядке для создания более надёжной связки. При этом обязательно соблюдаем технические зазоры между самими изделиями по 8-10 мм и между настилом и стенами по 15-20 мм;
- Места у стен дополняем меньшими фрагментами;
- Нумеруем все листы, чтобы не перепутать в процессе монтажа.
Чем обработать фанеру перед укладкой на пол, чтобы исключить возможность появления плесени и гниения? Для этого подойдёт любой антисептик по дереву для внутренних работ.
Образец подходящего антисептика
Этап №3: фиксация листов
И снова разберём два варианта в зависимости от основания:
- В случае с бетоном сверлим сначала фанеру с помощью дрели, затем отмечаем через отверстие точку на цементной поверхности, которую сверлим уже перфоратором.
В проём вставляем пластиковый дюбель, кладём древесно-слоистую плиту и фиксируем её стальным саморезом. И так по всему листу с шагом в 20 см;
Монтаж фанерных секций на бетонный пол
- Технология укладки фанеры на лаги немного отличается. С одной стороны можно выполнять крепление сразу саморезами, но с другой необходимо при этом попасть краем листа на середину балки, что доставляем дополнительные неудобства.
Монтаж фанеры на деревянные лаги
По окончанию работ шпаклюем все стыки и шляпки саморезов.
Вывод
Укладка фанеры на пол своими руками вполне осуществима. При этом не менее важным этапом является выбор подходящего материала.
Результат проделанных работ
Видео в этой статье ознакомит с дополнительными материалами.Если у вас возникли вопросы по изложенной теме, то вы можете задать их в комментариях.
Как укладывать фанеру для выравнивания деревянного пола под ламинат
Ламинат в настоящее время стал очень популярным вариантом напольного покрытия. Одним из достоинств материала, является возможность его укладки практически на любое основание после проведения необходимых подготовительных работ. Для владельцев деревянных домов или в случае, когда старое напольное покрытие из досок демонтировать крайне сложно, есть возможность укладки ламината на деревянное основание.
Постелить ламинат на деревянный пол довольно просто, только следует учесть, что необходимо ровное основание для укладки. Перепад высоты не должен превышать 2 мм. В связи с этим, зачастую, пол нужно выравнивать.
Один из простых и малозатратных способов подгонки до нужного уровня деревянного пола — это выравнивание листами фанеры. Этот вариант отлично скроет все неровности и дефекты основания.
Выбор фанеры для укладки под ламинат
Покупать фанеру под ламинат рекомендуется не тоньше 10 мм. Толщина листа фанеры в идеале должна быть больше, чем толщина чистового напольного покрытия. Также следует определиться и с маркой деревянного материала — она зависит от степени влагостойкости.
Для работ в жилых помещениях предназначены марки фанеры ФК и ФСФ. Листы ФСФ производятся с применением фенолформальдегидного клея. Они обладают хорошей влагостойкостью, но их использование внутри помещения не желательно, т. к. представляет вред для здоровья. Лучше отдать предпочтение менее влагостойкой, но при том экологичной и более дешевой марке ФК.
Для выравнивания основания пола подойдет сорт фанеры ¾ и 2/3. Лист должен быть отшлифован хотя бы с одной стороны. Фанера укладывается шлифованной стороной вверх и на нее настилается ламинат.
Плюсы и минусы выравнивания пола фанерой
Сглаживание перепадов высоты деревянного пола посредством укладки фанеры довольно универсальный способ ремонта основания перед настилом напольного покрытия.
- прочность и влагостойкость фанеры увеличивают срок службы ламината;
- звуко- и теплоизоляционные свойства материала;
- получение в результате качественного ровного и устойчивого основания;
- низкая цена материала и минимальные затраты на его монтаж;
- простота укладки позволяет быстро провести работы по выравниванию пола.
Есть, конечно, и один существенный недостаток использования данного материала. При выравнивании фанерой увеличивается высота настила, что для определенных помещений может быть недопустимо.
Способы укладки фанеры на деревянный пол
Существует два основных способа монтажа покрытия из фанеры на деревянный пол:
Монтаж листов фанеры с использованием лаг является наиболее трудоемким способом. В качестве лаг рекомендуется брать доски толщиной от 40 мм и шириной 80−100 мм. При установке соблюдать расстояние между осями не более 50 см. Лаги ставятся таким образом, чтобы их верхние точки находились в одной горизонтальной плоскости.
Листы фанерного покрытия укладываются на подобии кирпичной кладки, т. е. не должно быть пересечения 4-х швов в одном месте. Это делается для предотвращения деформации.
При укладке фанеры края листов располагаются на лагах и фиксируется саморезами с промежутками не более 30 см. При этом должно оставаться расстояние между листами — швы около 2-х мм.
Правильно установленное фанерное покрытие на основание из лаг будет устойчиво к воздействию влаги и тепла. Такой способ отлично скрывает большие перепады высоты пола. Однако, следует учесть, что для помещений с низкими потолками он не подходит, так как пол поднимается на 8−10 см.
Если деревянное основание не отличается большими перепадами высоты плоскости, то применим способ укладки фанеры на клей. Для выравнивания пола без использования лаг толщина листов фанеры должна быть от 12 мм. Начать работу следует с очистки основания от мусора и пыли. Нарезаем фанеру. Без закрепления настилаем на весь пол и подгоняем куски по размеру. Предварительно просверливаем отверстия под шурупы.
Затем листы можно убрать и подготовить основание — пропитать поверхность грунтовкой. При укладке каждый лист промазывается специальным клеем для фанеры слоем до 3-х мм и крепится на шурупы. Швы между листами должны быть 2−3 мм.
Таким способом ровное и прочное основание под финишную отделку пола быстро монтируется и не требует больших затрат.
Раскрой и примерка фанеры
Раскрой фанеры производится в соответствии с площадью пола. Необходимо учесть, что при укладке от стены делается отступ в 10 мм и зазор между швами 2−3 мм. Распилив листы на квадраты нужного размера, нужно проверить их края на предмет расслаивания с торцов и наличия прочих дефектов. Если край испорчен, заготовку следует заменить.
Укладка фанеры производится в шахматном порядке. Листы просверливаются к основанию саморезами по периметру и дополнительно по поверхности с шагом около 20 см. Для быстрого и удобного монтажа рекомендуется пронумеровать листы, а также наметить места крепления саморезами.
После примерки заготовки снимаются, основание очищается от грязи и пыли. Приготовленные листы перед укладкой, с целью увеличения срока службы, следует пропитать антисептиком. Затем можно приступать к монтажу.
Технология укладки фанеры
- Производится крепление фанеры к деревянному полу по заранее намеченной схеме расположения листов. Для крепления используются саморезы или шурупы с пластиковыми дюбелями. Отверстия под саморезы заранее просверливаются и зенкуются сверлом с большим диаметром, для того, чтобы «скрыть» шляпку шурупа.
- Смонтированное основание из фанеры под укладку ламината шлифуют, а затем покрывают защитными составами, повышающими влагостойкость и износостойкость.
- Поверх настилают специальную подложку для ламината, которая обладает шумопоглощающими, теплоизоляционными свойствами.
Технология выравнивания пола фанерой позволяет подготовить к укладке финишного покрытия деревянное основание любого качества. Если работы по монтажу чернового напольного покрытия из фанеры выполнены с соблюдением необходимых требований, то ламинат прослужит долгое время. Экологическая безопасность, неприхотливость, прочность материала дают возможность применять его в жилых помещениях для создания ровного и устойчивого пола.
Похожие статьи Пробковый пол – что это? Рассмотрим пробковый пол Доски для пола: размеры и эксплуатационные характеристики Характеристики и монтаж половых досок Пробковые полы:технология монтажа Обзор пробковых половПроизводственный процесс — ООО «Китроник»
Фанера — это панельный продукт на древесной основе, состоящий из набора шпона, склеенных смолой.
Для нас важно, чтобы все необработанные бревна, используемые в нашей фанере, поступали из законных и устойчивых лесных концессий. Для обеспечения этого мы используем только заводы, которые придерживаются Политики ответственных закупок Федерации торговли лесоматериалами.
Как только деревья достигают приемлемого уровня зрелости, их вырубают обученные сборщики урожая. В зависимости от работы мельницы, транспортные средства, подобные тем, что на изображении выше, могут использоваться для выбора и валки деревьев с использованием спутниковых изображений. Этап 2: Транспортировка на завод Бревна вывозятся из лесхоза на лесопилку для переработки.

Транспорт в некоторых случаях сопряжен со своими экологическими проблемами, поскольку лесные массивы вырубаются, чтобы освободить место для дорог, и поэтому новые деревья не могут расти. Этап 3: Бревенчатый пруд По прибытии на завод бревна хранятся на складе бревен. Заводы будут использовать различные методы для удержания влаги в бревнах, многие из которых выбирают спринклерные системы. Затем бревна в конечном итоге доберутся до бревенчатого пруда. Бревна погружают в воду на длительный период времени, чтобы их было легче распилить по размеру и легче чистить. На некоторых заводах в более холодном климате есть пруды с подогревом бревен, поскольку тепло также улучшает качество лущения; они называют это гидротермальной обработкой. Шаг 4. Окорка бревен
Перед распиловкой и лущением бревен необходимо удалить кору. Заводы используют такие промышленные машины для окорки бревен по мере их продвижения по производственной линии.

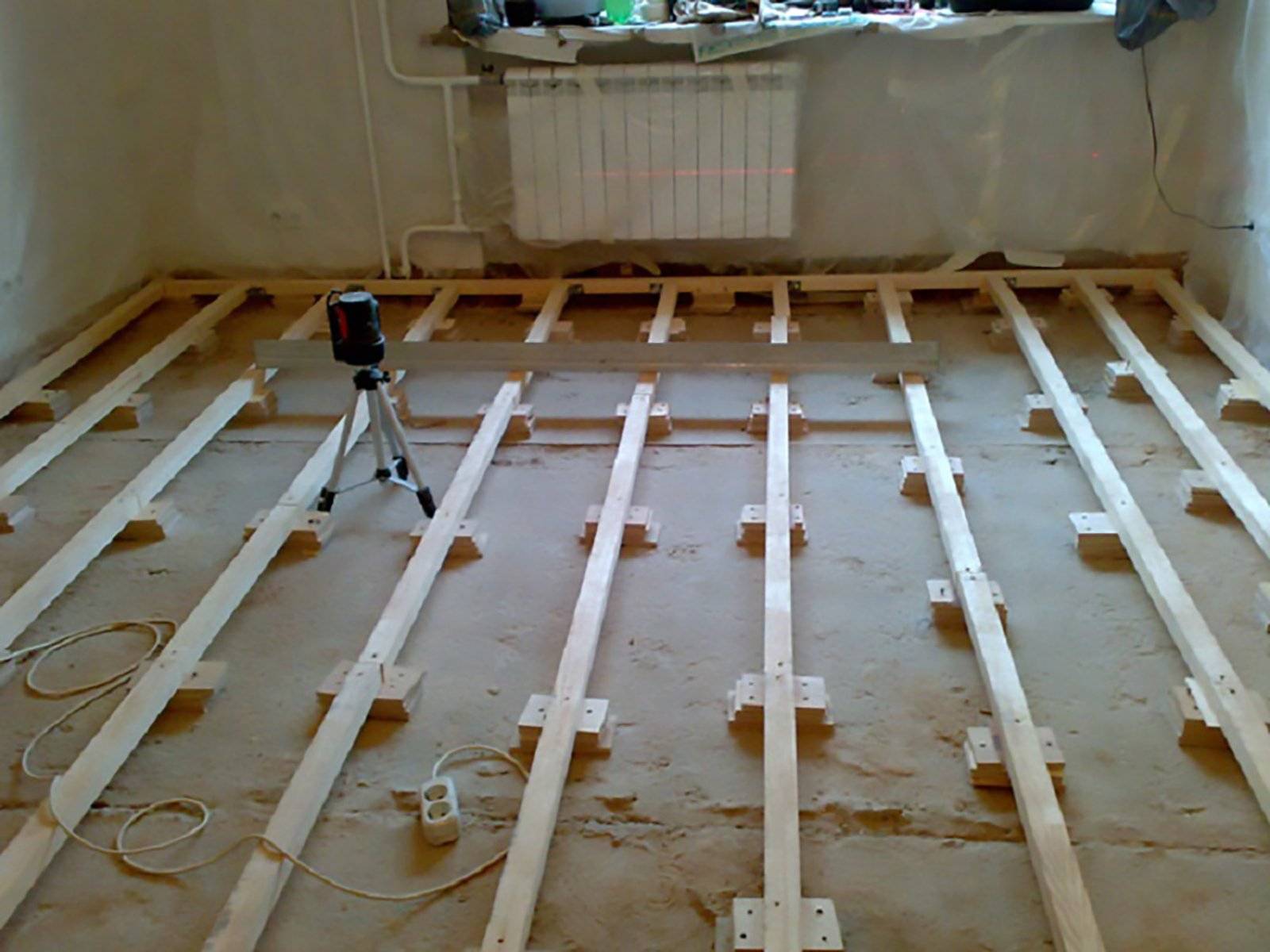
После лущения шпон длинными потоками перемещается по производственной линии. Их нужно обрезать по размеру и пройти первоначальный процесс сортировки. Сортировка особенно важна в отношении березовой фанеры (лазерной печати), поэтому большинство заводов используют технологию сканирования для проверки дефектов шпона, резки до необходимых размеров, а затем отделения потенциального лицевого шпона от основного шпона. В отличие от заводов из Восточной Европы и Прибалтики, такие страны, как Китай, будут лущить шпон на более мелкие квадраты, а затем сшивать их до соответствующего размера, что является более экономичным (но снижающим качество) методом.
Шаг 8. Сушка виниров На данный момент шпон еще влажный из-за замачивания в бревенчатом пруду. Виниры должны быть высушены по целому ряду причин; от защиты древесины от грибкового распада до повышения механических свойств готовой доски.

После высыхания виниры необходимо отремонтировать там, где есть дефекты. В случае с березовой фанерой, например, открытые сучки (там, где раньше были ветки) можно «заткнуть». Трещины в шпоне на фанере также можно заполнить, а шпон неподходящего размера можно срастить вместе (см. выше) . На некоторых фабриках есть машина, которая сканирует шпон и автоматически затыкает открытые отверстия или сучки. (См. ниже). Этап 10: Нанесение клея и укладка Виниры проходят через машину для склеивания, которая, по сути, наносит клей на лицевую и обратную стороны шпона.

Холодное прессование происходит после нанесения клея для подготовки виниров к горячему прессованию. Это помогает выровнять шпон и обеспечить равномерное распределение клея по шпону. Шаг 12: Горячее прессование (Daylight Press) На этом этапе производственного процесса собственно панели начинают обретать форму. Несколько панелей загружаются в пресс дневного света. Затем Daylight Press сжимает и поддерживает нагретое давление на доски в течение длительного периода времени. Это создает и поддерживает необходимый контакт между клеем и винирами. Это также уменьшает натяжение клеевого шва и толщину слоя клея. Шаг 13: Обрезка, шлифовка и окончательная обработка
После горячего прессования плиту оставляют для стабилизации и охлаждения перед дальнейшей обработкой.
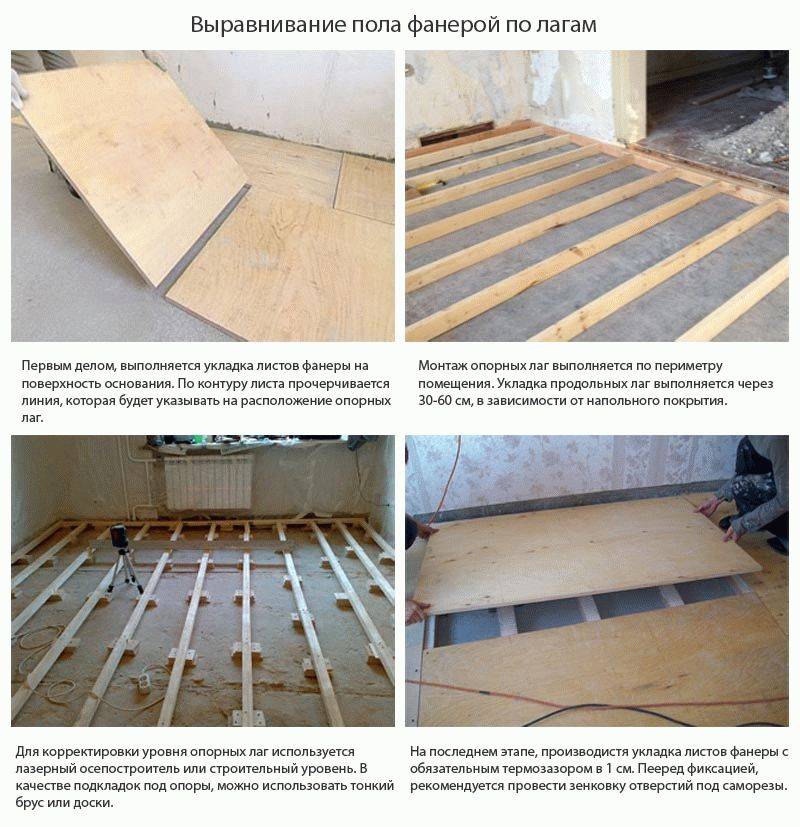
Затем готовые изделия складываются и соединяются вместе. Все соответствующие знаки CE напечатаны на упаковке.
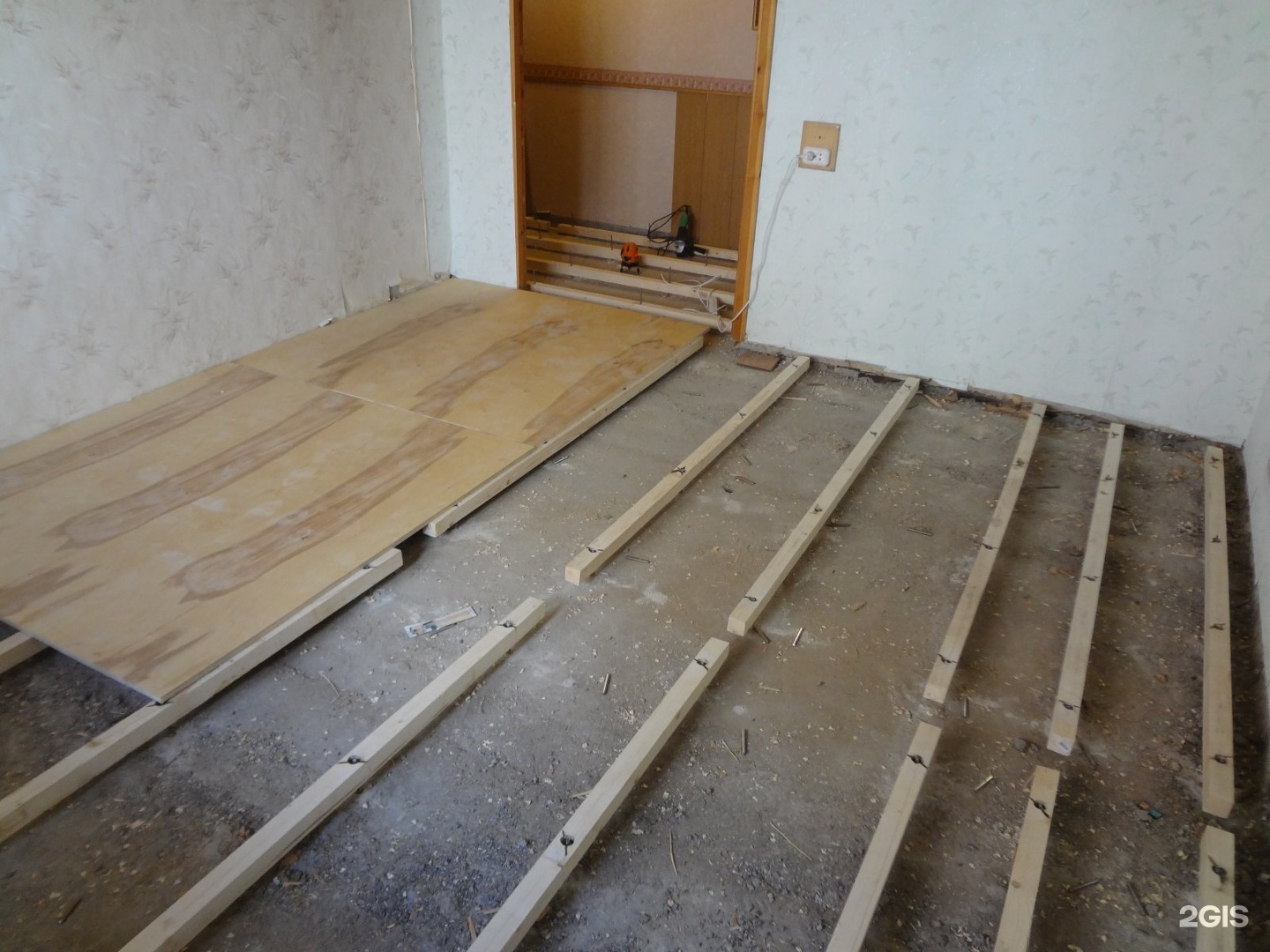
Завозим фанеру (laserply) еженедельно, готовую к отправке Вам!
©Kitronik Ltd. Вы можете распечатать эту страницу и дать ссылку на нее, но не должны копировать страницу или ее часть без предварительного письменного согласия компании Kitronik.
Как сделать фанеру?
Шон СюйШон Сюй
Предлагайте лучшие решения для моих клиентов.
Опубликовано 14 февраля 2019 г.
+ Подписаться
Сырье:
Наружные слои фанеры известны соответственно как лицевая и изнаночная стороны. Лицевая сторона — это поверхность, которую можно использовать или видеть, в то время как обратная сторона остается неиспользованной или скрытой. Центральный слой известен как ядро. В фанерах с пятью или более слоями промежуточные слои известны как поперечные полосы.
Фанера может быть изготовлена из лиственных пород, хвойных пород или их комбинации. Некоторые распространенные лиственные породы включают ясень, клен, красное дерево, дуб и тик. Наиболее распространенной хвойной древесиной, используемой для изготовления фанеры в Соединенных Штатах, является пихта Дугласа, хотя также используются несколько разновидностей сосны, кедра, ели и красного дерева.
Многослойная фанера имеет сердцевину из древесно-стружечных плит или цельных пиломатериалов, соединенных встык. Лицевая и оборотная стороны отделаны шпоном фанеры. Композитная фанера используется там, где нужны очень толстые листы.
Тип клея, используемого для склеивания слоев древесины, зависит от конкретного применения готовой фанеры. Листы фанеры хвойных пород, предназначенные для установки на внешней стороне конструкции, обычно используют фенолформальдегидную смолу в качестве клея из-за ее превосходной прочности и устойчивости к влаге. В листах фанеры из хвойных пород, предназначенных для установки внутри конструкции, может использоваться клей с белком крови или соевым белком, хотя большинство внутренних листов из хвойной древесины в настоящее время изготавливаются из той же фенолформальдегидной смолы, которая используется для наружных листов. Фанера из твердой древесины, используемая для внутренних работ и изготовления мебели, обычно изготавливается из карбамидоформальдегидной смолы.
В некоторых случаях требуются фанерные листы с тонким слоем бумаги или ткани, пропитанной пластиком, металлом или смолой, приклеенной либо к лицевой, либо к тыльной стороне (или к обоим), чтобы придать внешней поверхности дополнительную устойчивость к влаге и истиранию или улучшить ее краскоудерживающие свойства. Такая фанера называется фанерой с покрытием и обычно используется в строительстве, на транспорте и в сельском хозяйстве.
Прочие фанерные листы могут быть покрыты жидким красителем для придания поверхности законченного вида или могут быть обработаны различными химическими веществами для повышения огнестойкости фанеры или устойчивости к гниению.
Классификация и классификация фанеры:
Существует два широких класса фанеры, каждый из которых имеет собственную систему классификации.
Один класс известен как строительный и промышленный. Фанера этого класса используется в первую очередь из-за ее прочности и оценивается по способности подвергаться воздействию внешних факторов и типу шпона, используемого на лицевой и тыльной сторонах. Возможность воздействия может быть внутренней или внешней, в зависимости от типа клея. Сорта шпона могут быть N, A, B, C или D. У сорта N очень мало поверхностных дефектов, а у сорта D может быть много сучков и трещин. Например, фанера, используемая для чернового пола в доме, имеет рейтинг «Интерьер C-D». Это означает, что у него лицевая сторона C, а оборотная сторона D, и клей подходит для использования в защищенных местах. Внутренние слои всей строительной и промышленной фанеры изготавливаются из шпона класса С или D, независимо от сорта.
Другой класс фанеры известен как твердая древесина и декоративная. Фанера этого класса используется в первую очередь из-за ее внешнего вида и классифицируется в порядке убывания влагостойкости как техническая (внешняя), тип I (внешняя), тип II (внутренняя) и тип III (внутренняя). Их лицевые виниры практически не имеют дефектов.
Производство:
ПроцессДерева, используемые для производства фанеры, обычно меньше в диаметре, чем те, которые используются для производства пиломатериалов. В большинстве случаев они были посажены и выращены на территориях, принадлежащих фанерной компании. Эти области тщательно обрабатываются, чтобы максимизировать рост деревьев и свести к минимуму ущерб от насекомых или пожара.
Вот типичная последовательность операций по переработке деревьев в стандартные фанерные листы размером 4 фута на 8 футов (1,2 м на 2,4 м):
Бревна сначала окорываются, а затем разрезаются на лущильные блоки. Для того чтобы нарезать блоки на полосы шпона, их сначала замачивают, а затем очищают от шпона.
- 1 Выбранные деревья в районе отмечены как готовые к вырубке или вырубке. Рубка может производиться цепными пилами с бензиновым двигателем или большими гидравлическими ножницами, установленными на передней части колесных транспортных средств, называемых валочными машинами. Ветки удаляют с поваленных деревьев цепными пилами.
- 2 Обрезанные стволы деревьев или бревна перетаскиваются на погрузочную площадку колесными транспортными средствами, называемыми скиддерами. Бревна нарезаются по длине и загружаются в грузовики для перевозки на фанерный завод, где они складываются в длинные штабели, известные как бревенчатые настилы.
- 3 По мере необходимости бревна подбираются с бревенчатых полок погрузчиками на резиновых колесах и помещаются на цепной конвейер, который доставляет их к окорочной машине. Эта машина удаляет кору либо с помощью шлифовальных кругов с острыми зубьями, либо с помощью струй воды под высоким давлением, в то время как бревно медленно вращается вокруг своей длинной оси.
- 4 Окоренные бревна доставляются на лесопилку по цепному конвейеру, где огромная циркулярная пила разрезает их на секции длиной от 8 футов 4 дюймов (2,5 м) до 8 футов 6 дюймов (2,6 м), подходящие для изготовления стандарта 8. футов (2,4 м) длинных листов. Эти секции бревна известны как блоки-пилеры.
- 5 Перед тем, как резать шпон, необходимо нагреть и замочить блоки для снятия шпона, чтобы смягчить древесину. Блоки можно пропаривать или погружать в горячую воду. Этот процесс занимает от 12 до 40 часов в зависимости от породы дерева, диаметра блока и других факторов.
- 6 Затем нагретые блоки отслаивателя транспортируются к токарному станку, где они автоматически выравниваются и подаются в токарный станок по одному. Когда токарный станок быстро вращает блок вокруг своей длинной оси, лезвие ножа во всю длину отделяет непрерывный лист шпона от поверхности прядильного блока со скоростью 300–800 футов/мин (90–240 м/мин).
Когда диаметр блока уменьшается примерно до 3–4 дюймов (230–305 мм), оставшийся кусок дерева, известный как сердцевина лущильного станка, выталкивается из токарного станка, и на его место подается новый блок лущильного станка.
- 7 Длинный лист шпона, выходящий из лущильного станка, может быть немедленно обработан или может храниться в длинных многоярусных лотках или наматываться на рулоны. В любом случае следующий процесс включает в себя нарезку шпона на полезную ширину, обычно около 4 футов-6 дюймов (1,4 м), для изготовления стандартных фанерных листов шириной 4 фута (1,2 м). При этом оптические сканеры ищут участки с недопустимыми дефектами и вырезают их, оставляя куски шпона меньше стандартной ширины.
- Влажные полосы шпона сматываются в рулон, при этом оптический сканер выявляет любые недопустимые дефекты древесины. После высыхания шпон сортируется и укладывается. Выбранные участки шпона склеиваются. Горячий пресс используется для запечатывания шпона в один цельный кусок фанеры, который будет обрезан и отшлифован перед штамповкой соответствующей марки.
- 8 Затем секции шпона сортируются и укладываются в штабели в соответствии с сортом. Это можно сделать вручную или автоматически с помощью оптических сканеров.
- 9 Отсортированные секции подаются в сушилку, чтобы уменьшить их влажность и дать им усадку, прежде чем они будут склеены. Большинство фанерных заводов используют механическую сушилку, в которой куски непрерывно перемещаются через нагретую камеру. В некоторых сушилках струи высокоскоростного нагретого воздуха обдувают поверхность изделий, чтобы ускорить процесс сушки.
- 10 Когда секции шпона выходят из сушилки, они укладываются в штабели в соответствии с сортами. Секции нижней ширины имеют дополнительный шпон, соединенный лентой или клеем, чтобы сделать детали пригодными для использования во внутренних слоях, где внешний вид и прочность менее важны.
- 11 Те участки шпона, которые будут укладываться в поперечном направлении — сердцевина в трехслойных листах или поперечные полосы в пятислойных листах — нарезаются на куски длиной примерно 4 фута-3 дюйма (1,3 м).
- 12 Когда соответствующие участки шпона собраны для определенного сортамента фанеры, начинается процесс укладки и склеивания кусков вместе. Это может быть сделано вручную или полуавтоматически с машинами. В простейшем случае трехслойных листов задний шпон укладывают ровно и пропускают через клеераспределитель, который наносит слой клея на верхнюю поверхность. Затем короткие отрезки основного шпона укладывают поперек поверх приклеенной спинки, и весь лист повторно пропускают через клеераспределитель. Наконец, лицевой шпон укладывается поверх склеенной сердцевины, и лист укладывается вместе с другими листами, ожидающими отправки в пресс.
- 13 Склеенные листы загружаются в многоярусный горячий пресс. прессы могут обрабатывать 20-40 листов за раз, при этом каждый лист загружается в отдельный слот. Когда все листы загружены, пресс сжимает их вместе под давлением примерно 110–200 фунтов на кв. дюйм (7,6–13,8 бар), одновременно нагревая их до температуры примерно 230–315° F (109,9–157,2° С).
Давление обеспечивает хороший контакт между слоями шпона, а тепло способствует правильному отверждению клея для достижения максимальной прочности. Через 2-7 минут пресс открывается и листы выгружаются.
- 14 Затем необработанные листы проходят через набор пил, которые обрезают их до конечной ширины и длины. Листы более высокого качества проходят через набор ленточных шлифовальных машин шириной 4 фута (1,2 м), которые шлифуют как лицевую, так и тыльную сторону. Листы промежуточного сорта шлифуются вручную точечно, чтобы убрать шероховатости. Некоторые листы пропускаются через набор циркулярных пил, которые прорезают неглубокие канавки на лицевой стороне, чтобы придать фанере текстурированный вид. После окончательной проверки все оставшиеся дефекты устраняются.
- 15 На готовые листы наносится клеймо сорта, которое дает покупателю информацию о рейтинге выдержки, сорте, заводском номере и других факторах. Листы одного сорта и товарного знака связываются вместе в стопки и перемещаются на склад в ожидании отгрузки.
Полезные советы для всех моих клиентов в этот период
5 марта 2020 г.
Производство древесно-стружечных плит-IV
18 ноября 2019 г.
Производство древесно-стружечных плит-III
12 ноября 2019 г.
Производство древесно-стружечных плит-II
2 ноября 2019 г.
Производство древесно-стружечных плит
29 окт. 2019 г.
Принцип работы машины для формовки матов
11 сент. 2019 г.
Процесс производства ДСП
27 июня 2019 г.
Как сделать МДФ?
20 февраля 2019 г.